Top 10 Most Common Workplace Hazards and How to Stop Them Becoming Accidents
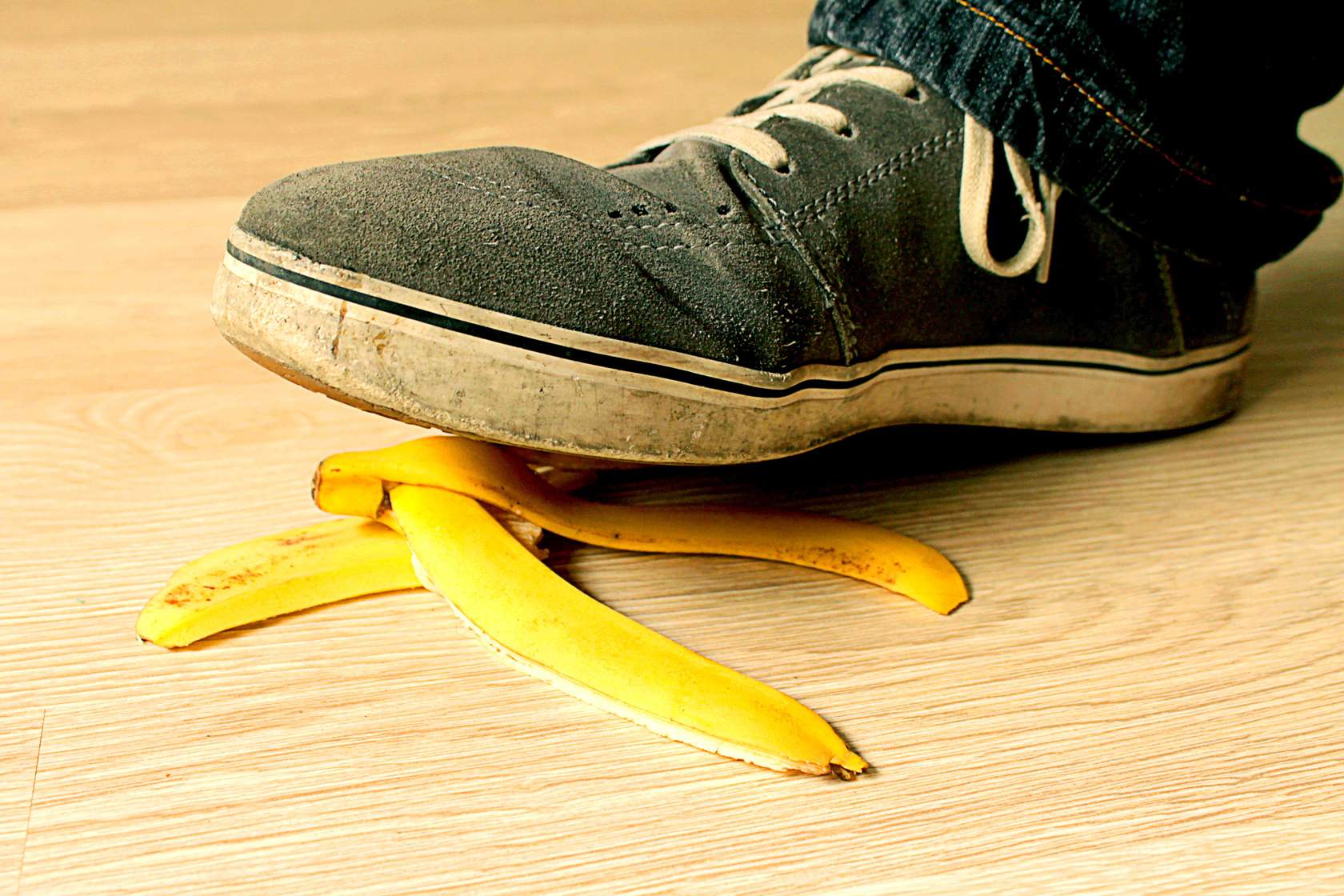
Creating a safe workplace is an essential responsibility, and understanding common hazards is the first step in this process. Let’s delve deeper into the top 10 workplace hazards and explore practical strategies to mitigate them.
1. Slips, Trips, and Falls
The Culprits: These are often caused by wet or oily surfaces, occasional spills, loose rugs or mats, and cluttered pathways.
The Fix: Implement regular cleaning protocols and immediately address spills. Use anti-slip floor tape and mats in prone areas. Keep walkways and work areas free of clutter. Ensure adequate lighting so that employees can see and avoid obstacles. Training staff on proper housekeeping methods can significantly reduce these incidents.
2. Ergonomic Hazards
The Culprits: Poor workstation ergonomics, repetitive tasks, and awkward postures can lead to musculoskeletal disorders.
The Fix: Ergonomic assessments of workstations are crucial. Adjustable chairs, desks, and monitor stands can help tailor the workspace to individual needs. Encourage micro-breaks every hour to reduce strain. Providing ergonomic tools, like vertical mice and ergonomic keyboards, can also help. Additionally, training on proper posture and lifting techniques is essential.
3. Electrical Hazards
The Culprits: These include exposed wiring, faulty equipment, and overloaded circuits.
The Fix: Conduct regular electrical safety checks. Ensure all electrical installations comply with safety standards. Use circuit breakers and ground fault circuit interrupters. Train employees to recognize electrical hazards and report them immediately. Regular maintenance of electrical equipment is also crucial to prevent malfunctions.
4. Chemical Hazards
The Culprits: Mishandling of chemicals, improper storage, and lack of knowledge can lead to serious injuries.
The Fix: Store chemicals properly with clear labeling. Provide Safety Data Sheets for all chemicals and train employees on how to read and understand them. Ensure proper ventilation in areas where chemicals are used. PPE such as gloves, goggles, and respirators should be readily available and mandatory for use.
5. Fire Hazards
The Culprits: Common causes include electrical malfunctions, flammable materials, and careless smoking.
The Fix: Regularly inspect electrical systems and dispose of faulty equipment. Store flammable materials safely and away from ignition sources. Implement a strict no-smoking policy. Regular fire drills and training on using fire extinguishers can prepare employees for emergencies.
6. Biological Hazards
The Culprits: These include exposure to bacteria, viruses, and fungi, often in healthcare, laboratory, or outdoor work.
The Fix: Enforce strict hygiene practices like handwashing. Provide appropriate PPE, such as gloves and face masks. Regular cleaning and disinfection of surfaces are crucial. Ensure proper vaccination for employees working in high-risk areas.
7. Noise Hazards
The Culprits: Constant exposure to loud machinery or work in acoustically active environments can lead to hearing loss.
The Fix: Provide hearing protection like earplugs or earmuffs. Implement sound-dampening measures in noisy areas. Regular hearing tests for employees can help monitor any changes in hearing ability. Limiting exposure time to noisy environments is also a practical approach.
8. Physical Hazards
The Culprits: These are environmental factors like radiation, extreme temperatures, and sunlight exposure.
The Fix: Use shielding materials to reduce exposure to radiation. Implement cooling systems or provide insulated clothing for extreme temperatures. For outdoor workers, provide sunscreen, hats, and appropriate clothing to protect from sun exposure.
9. Psychosocial Hazards
The Culprits: Stress, workplace bullying, and violence can have serious impacts on mental health.
The Fix: Create policies that promote a healthy work-life balance. Provide resources for mental health support. Encourage open communication and have a zero-tolerance policy for bullying and harassment. Training in stress management and conflict resolution can be beneficial.
10. Safety Hazards
The Culprits: Inadequate machine guarding, poor maintenance, and lack of safety training are primary concerns.
The Fix: Ensure all machines have appropriate guards and safety features. Regular maintenance checks are crucial to ensure equipment is in good working order. Provide comprehensive safety training for all employees, focusing on the specific hazards of their job roles.
Creating a safe work environment is an ongoing process, and staying informed about potential hazards is a key part of that journey. At Fit2Trade, we understand the complexities of workplace safety and by using our scheduled H&S routines, you get real-time visibility that daily, weekly and monthly safety checks have been completed.
For more insights and resources, visit us at Fit2Trade.com. Remember, a proactive approach to safety can make all the difference in creating a healthy and secure work environment.
Written by Rory Byrne from Fit2Trade